耐火材料的耐磨性是指材料在高温环境下抵抗机械磨损、冲刷和化学侵蚀的能力。这一特性对冶金、玻璃、陶瓷等高温工业中的设备保护至关重要。耐火材料的耐磨性由其组成和结构决定,具体影响因素如下:
一、耐火材料组成对耐磨性的影响
化学成分
氧化物:耐火材料通常由一种或多种氧化物构成,如氧化铝(Al₂O₃)、氧化镁(MgO)、氧化硅(SiO₂)等。氧化铝和氧化镁等高熔点氧化物提高了材料的高温硬度和耐磨性。
氧化铝:高硬度和高熔点,广泛用于需要高耐磨性的场合。
氧化镁:具有优异的高温稳定性和抗渣性,常用于钢铁冶炼等高温腐蚀环境。
碳化物:如碳化硅(SiC)、碳化硼(B₄C)等,因其高的硬度和耐高温性能,在磨损严重的环境下表现良好。
碳化硅:很高的硬度和耐磨性,适用于高磨损的炉衬、滑道等部位。
碳化硼:高硬度和良好的抗氧化性能,应用于恶劣环境。
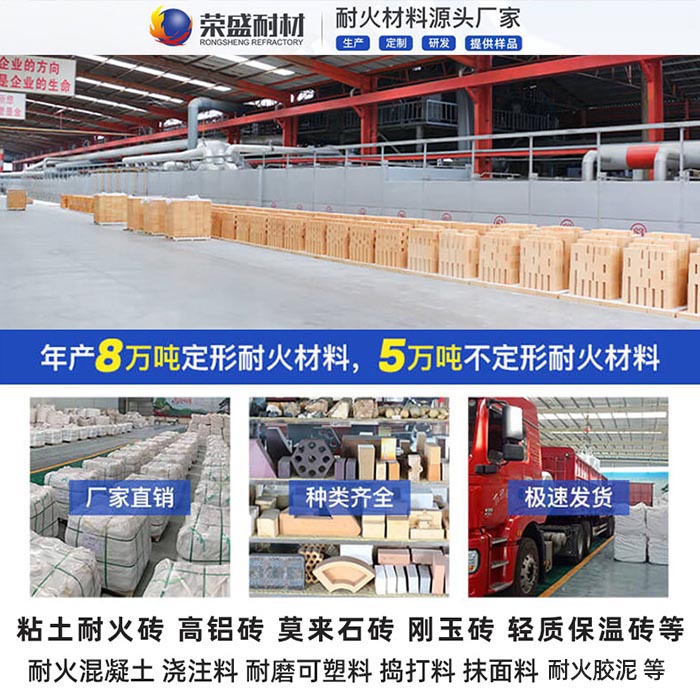
相组成
单相材料:纯氧化物或碳化物,如纯刚玉(Al₂O₃)砖,具有较为均匀的物理和化学性能。
复合材料:由多种成分组成,通过微结构优化,如刚玉-莫来石(Al₂O₃-SiO₂)复合砖,结合多种相的优点,提升材料的整体耐磨性能。
添加剂
金属氧化物:如氧化铬(Cr₂O₃)、氧化钛(TiO₂)等,可通过改变晶体结构或形成强化相提高耐磨性。
碳质添加剂:如石墨,能增强材料的抗热震性和耐磨性,但也会影响抗氧化性能。
二、耐火材料结构对耐磨性的影响
晶相和晶粒
晶相组成:材料中的主要晶相决定了其耐磨性。如刚玉砖主要由刚玉晶相组成,提供了高硬度和耐磨性。
晶粒大小:细小均匀的晶粒结构有助于提高耐磨性,大晶粒结构可能导致脆性加大,耐磨性下降。
晶粒形貌:针状或片状晶粒可以提高材料的抗冲击能力,但也可能导致在某些方向上的弱化。
微观结构
致密度:高致密度材料通常具有较高的耐磨性,因为孔隙度低减少了磨损过程中材料表面的削弱。
显微组织:均匀细小的显微组织结构能够更有效地分散应力,减少局部应力集中导致的破坏。
结合相和杂质
结合相:陶瓷结合相或玻璃结合相的存在可影响材料的整体耐磨性,结合相强度越高,耐磨性越好。
杂质:如Fe₂O₃等杂质会影响材料的纯度和性能,降低耐磨性。
孔隙和微裂纹
孔隙:材料中的孔隙减少了有效承载面积,降低了耐磨性,高温下孔隙中的气体膨胀还可能导致材料开裂。
微裂纹:微裂纹会在材料受力时扩展,导致磨损加剧。
三、耐磨性测试与应用
测试方法
摩擦磨损试验:通过摩擦试验仪测量材料在特定条件下的磨损量。
冲击磨损试验:模拟高温下材料受到冲击的磨损情况。
高温腐蚀试验:在高温化学环境中测试材料的耐磨性和抗腐蚀性。
典型应用
冶金工业:高炉炉衬、转炉炉衬、电炉炉壁等需要高耐磨材料来抵抗铁水、钢水的冲刷和侵蚀。
水泥工业:回转窑内衬要求高耐磨性,以应对窑料的高温磨蚀。
玻璃工业:熔窑内衬材料需要耐受玻璃液的高温腐蚀和磨损。
四、优化与未来发展方向
材料优化
改性:通过添加微量元素或增强相,优化材料的组成和结构,提高耐磨性。
纳米技术:应用纳米材料和纳米技术改性传统耐火材料,提升其耐磨性和综合性能。
制造技术
烧结工艺:优化烧结温度和工艺参数,减少孔隙率,提高材料致密度。
复合工艺:采用多相复合材料设计,提高材料的综合耐磨性和耐高温性能。
环保与可持续性
绿色材料:开发低污染、可回收的耐火材料,减少对环境的影响。
再生利用:推动耐火材料的再生利用,减少资源浪费和环境负担。
耐火材料的耐磨性主要取决于其化学组成和微观结构。通过优化材料的化学成分、晶相结构和显微组织,可以显著提高材料在高温环境下的耐磨性。未来,随着材料科学的进步和制造工艺的提升,耐火材料的耐磨性能将进一步增强,以满足日益复杂和严苛的工业需求。
- 上一篇:防止耐火砖损伤的有效措施
- 下一篇:没有资料
新闻推荐